Advanced Polymer Chemistry Under One Umbrella
Advanced Polymer Chemistry Under One Umbrella
Skyi Composites
Strength. Stability. Sustainability.
Long Fiber Thermoplastics (LFTs) offer durability with UV, oxidation, and stress resistance, while processing aids optimize flow and crystallization for efficient production.
Fiber-Matrix Reinforcing
Engineering the Future of Sustainable Polymers
Skyi combines cutting-edge science with decades of expertise to develop high-performance polymer materials. Our mastery of fiber-matrix interactions, morphology, and rheology drives breakthroughs in durability, lightweighting, and recyclability.
Skyi FKuR Biopolymers
Biodegradable. Compostable. Bio-based.
Safe for people and the planet, our materials meet global sustainability goals and strict regulations, replacing conventional plastics responsibly.
Low-Carbon Footprint
Redefining Polymers for a Sustainable Tomorrow
By combining Skyi’s production excellence with FKuR’s material innovations, we create high-performance, eco-friendly polymers that support a circular and sustainable economy.
Unique Material Development
Our approach simplifies the complexity of material science—starting with in-depth analysis and culminating in flawless production.
Analysis
Comprehensive material and performance analysis to ensure optimal solutions tailored to your specific needs and requirements.
Prototyping
Rapid prototyping to validate designs, test functionality, and ensure readiness for full-scale composite production.
Engineering
Expert engineering for innovative composite designs, optimizing performance, durability, and cost-effectiveness in every project.
Production
Delivering High-Quality Composite Solutions with Precision Manufacturing and Strategic Support.
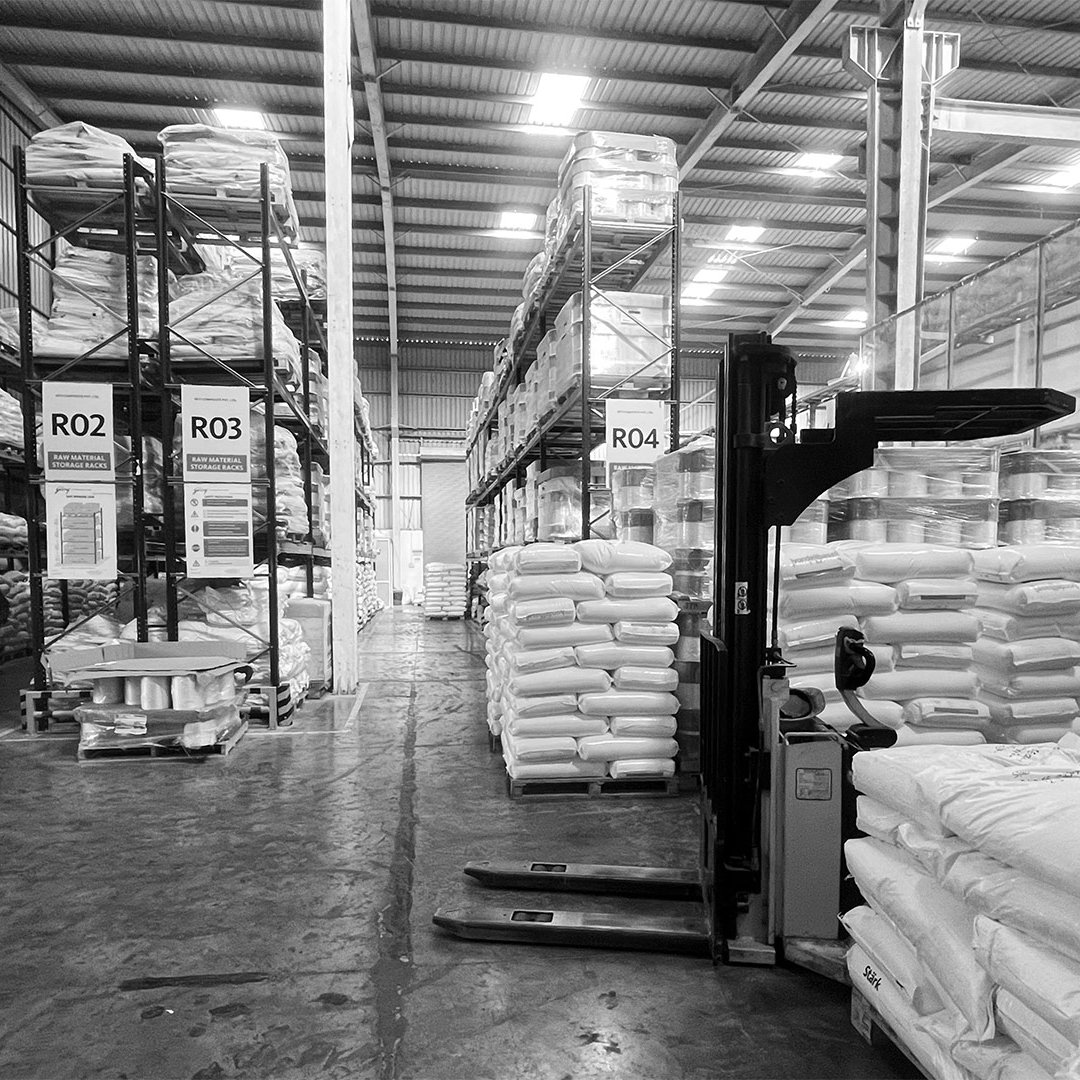
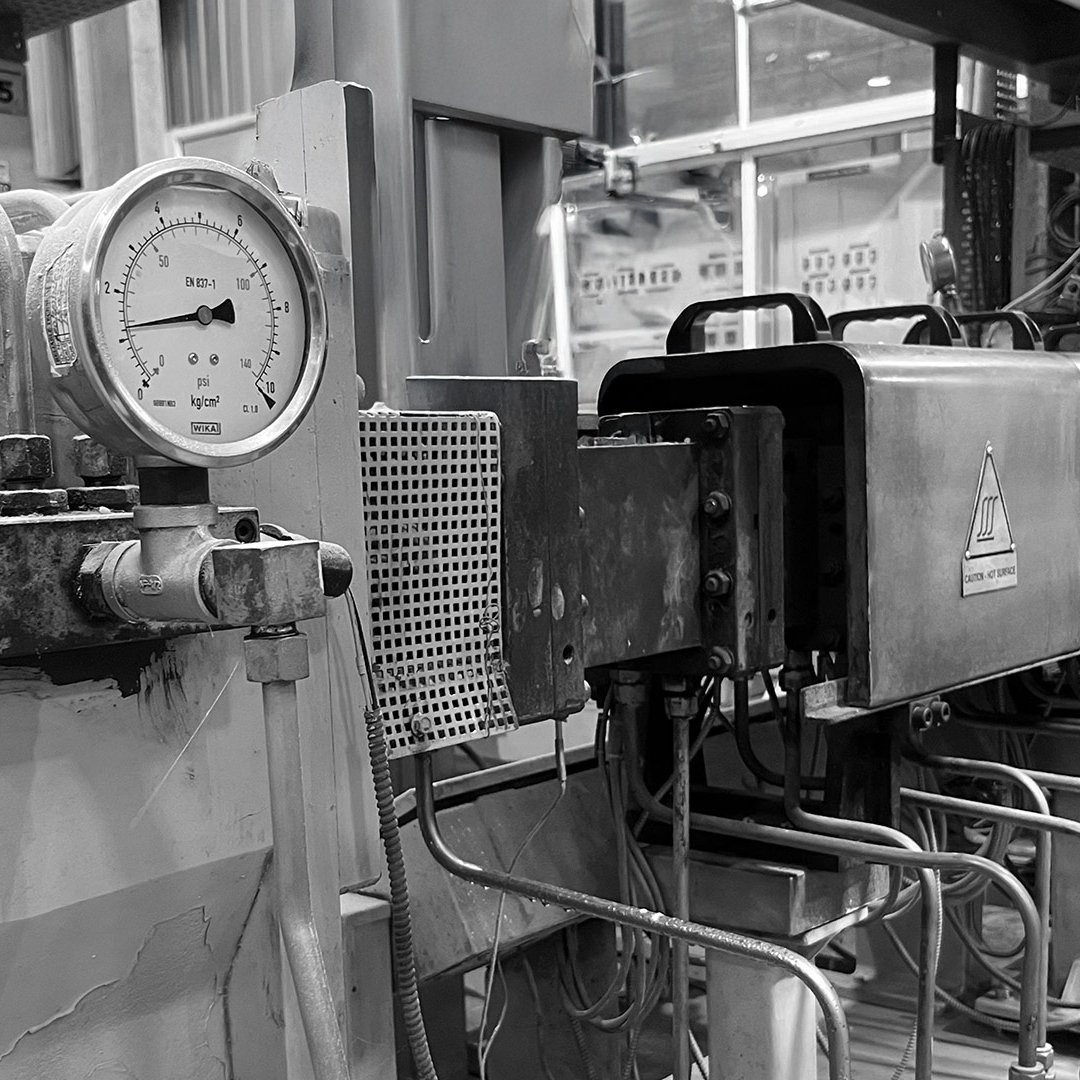
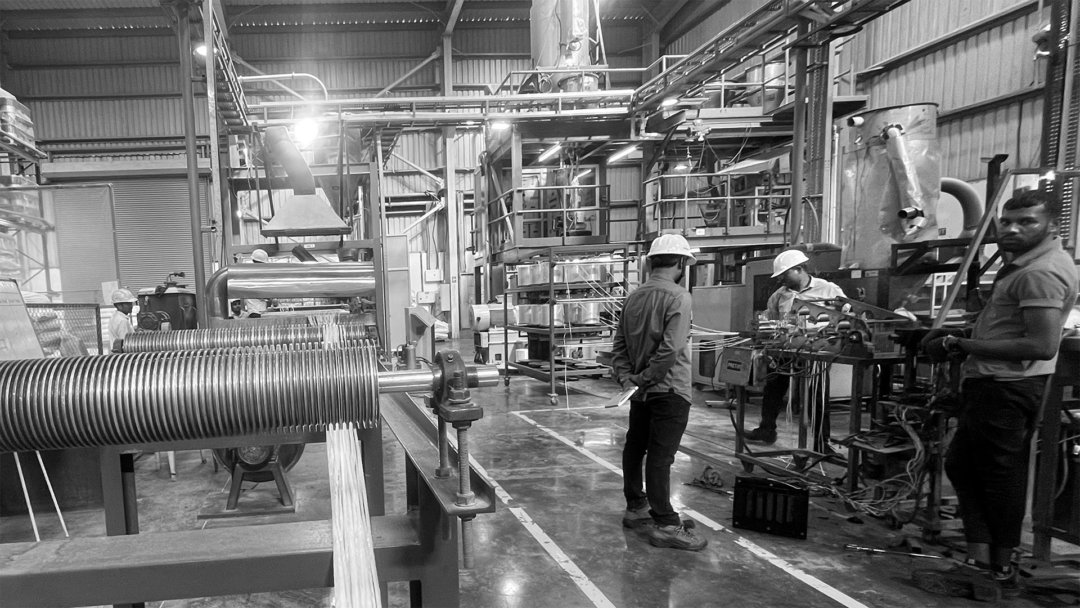
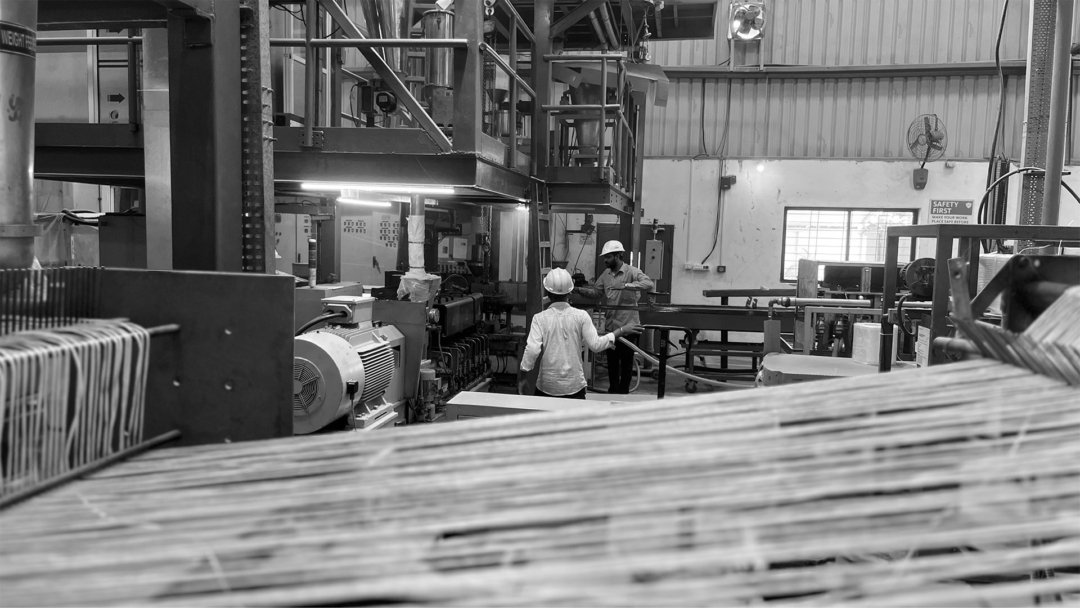
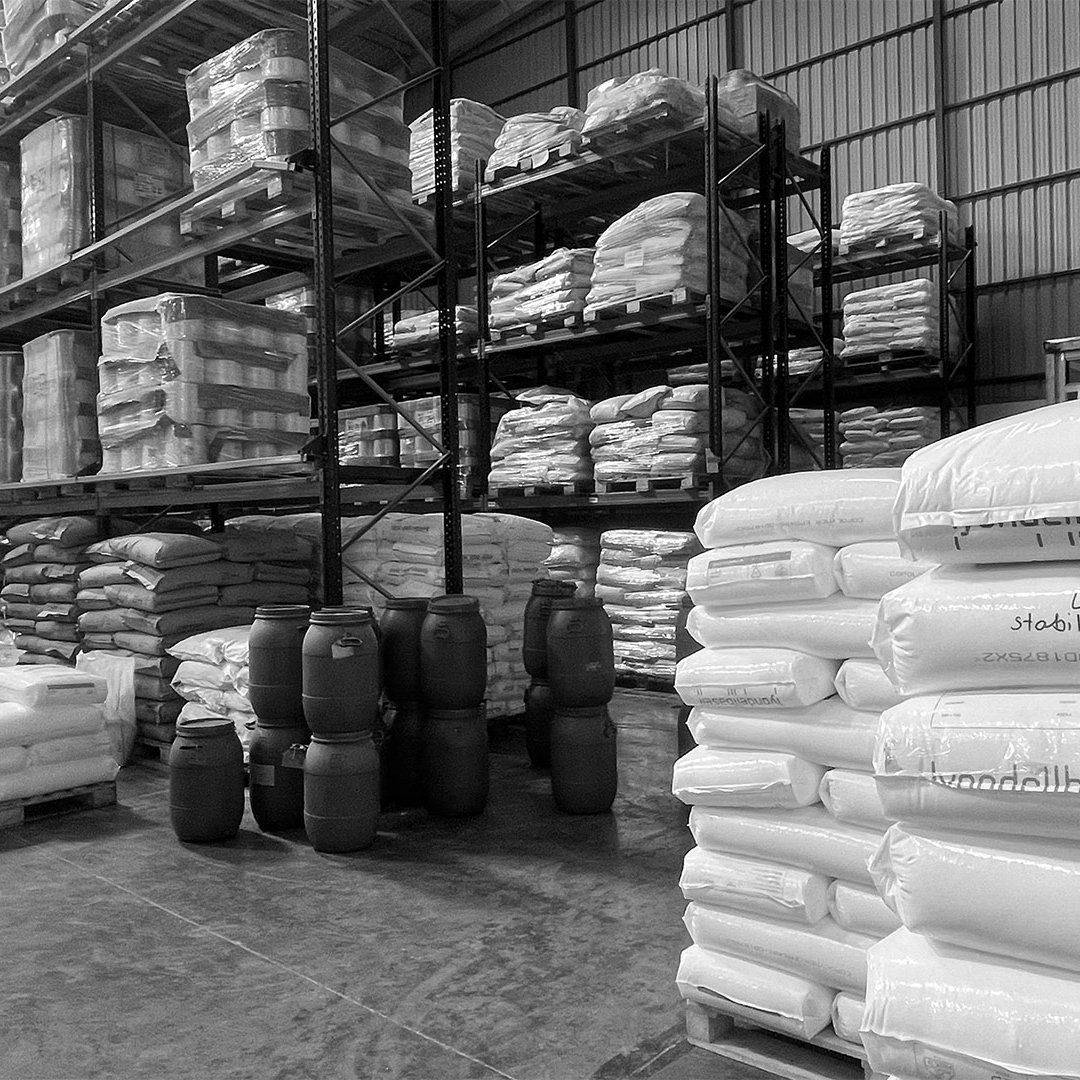
Our Composite MFG Facility
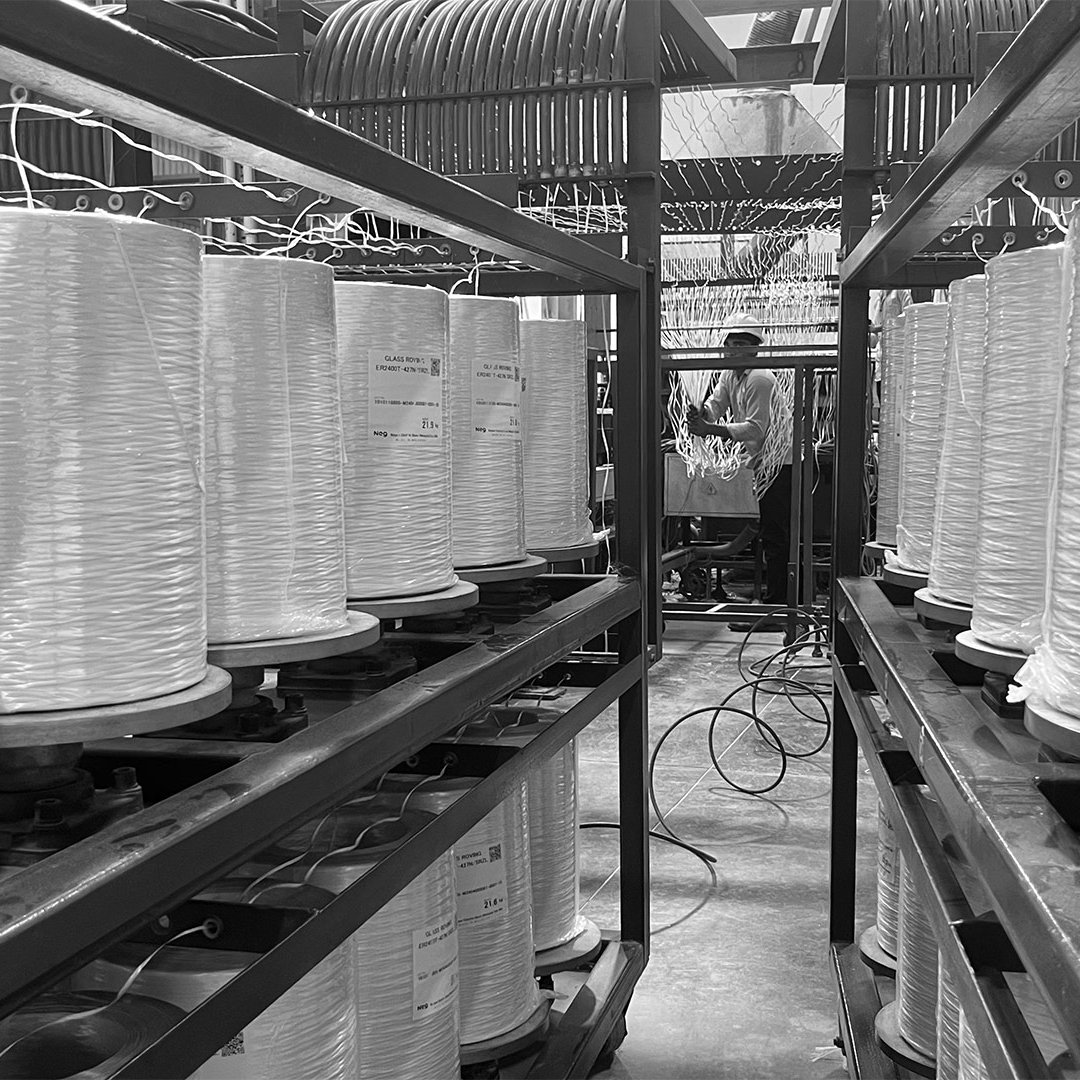
Skyi's international partnerships fuel innovation, foster research collaborations, and push the boundaries of material science.
AZL Aachen GmbH
Skyi is the only Indian company associated with AZL, a prestigious European consortium for lightweighting technologies. This collaboration provides access to cutting-edge advancements in lightweight materials and fosters pioneering innovations.
National Chemical Laboratory
Our collaboration with NCL focuses on developing functional polymers using hyperbranched chemistry. This partnership combines Skyi’s expertise in materials science with the Laboratory's research strengths to drive innovation in polymer technology.
FKuR GmbH
Our partnership with FKuR GmbH makes us the largest supplier of biocompostable materials in Southeast Asia. We provide sustainable solutions for films, packaging, laminates, and molded applications, accelerating the shift to eco-friendly alternatives.